
By Seth Mercer on Dec 3, 2021 1:48:27 PM
Hindsight is always 20/20! The afterthought usually occurs suddenly and with newfound clarity, though the particular circumstances may vary. There were probably some red flags you should have picked up on or taken more seriously.
Maybe you find yourself standing on the side of the road taking in the pungent aroma of the smoke as it rolls out from under the hood or listening with finely tuned attention to the waning whistle of the last air escaping from your tire. Perhaps you’re on your hands and knees with a sudden and captivating interest in your truck’s undercarriage or leaning over the engine exploring its furthest and deepest cavities with a flashlight.
Whatever the situation is, it's too late. That screech, rattle, grind, squeal, clunk, thud, click, or tick your truck was making was probably something you should have investigated sooner or had checked out instead of turning up the music a little louder and ignoring it.
Listen to the Sounds & Look for Warning Signs
It’s no different when it comes to hoppers and chutes at the plant or in the pit. The distinct clattering sound of material flowing through these vessels is a part of your operation. However, you need to pay attention when the sound changes and becomes muffled; it likely indicates that the vessel is becoming packed with material buildup on the inside walls or at the discharge point.
Ignore this subtle change in sound and you risk being left standing next to an idle process in need of emergency maintenance as normal flow stops and material begins spilling over the edge or backing up on conveyors.
Unplanned downtime is the equivalent of being stranded on the side of the road. In either situation, all of your momentum and progress has ground to a sudden and unexpected halt, and the desperate urge to get up and running and back on track again ASAP quickly kicks in.
When we’re forced to act quickly to resolve problems where hazards are present we can put ourselves in situations that invite risks and consequences that simply aren’t acceptable. Tackling the problem without the proper tools, procedures, or training can quickly get us into worse trouble yet.
When reacting to clear a blockage or proactively managing the material flow to , eliminating the need for any manual efforts is the approach best taken. Whether working from above, below, or within, the sudden dislodgement and movement of large volumes of material represents an unnecessary crush or entrapment risk to workers with costly consequences.
Creative problem solving from outside of the hopper or chute can compound problems as well. A brute force applied to the exterior with mallets or other implements of destruction will loosen material buildup. However, as the vessel walls become scarred by these strikes, the bumps and ridges they leave provide points for additional material accumulation to build more rapidly on.
Air lancing is a common practice to clear blockages, but reacting to these problems incurs the expense of time and money to regularly monitor and manually clear the chute or hopper while still leaving open the possibility of injury and downtime.
Proactive, preventative solutions—much like regular oil changes, tire rotations, and multi-point inspections—provide the safest, most reliable, and cost-effective approach to managing proper material flow, mitigating buildup, and avoiding unplanned maintenance and downtime.
Improve Material Flow & Prevent Blockages
Flow aids, such as and industrial vibrators, are effective and reliable tools that keep workers out of harm’s way while preventing material buildup, maximizing production, and keeping operating costs down.
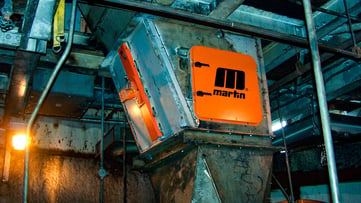
A broad range of rotary and linear of different sizes and force outputs deliver energy precisely where needed to reduce friction and break up material to keep it moving to the discharge opening. These devices mimic the action of a hammer blow with greater accuracy and without damaging the chute or hopper. Units can be electric-, pneumatic-, or hydraulic-powered.
use powerful, controlled blasts of air to dislodge material as it builds up on the interior walls of a hopper or chute. Air cannons consist of an air reservoir, a fast-acting valve with a trigger mechanism, and a nozzle to direct and distribute the air in the desired cleaning pattern. These systems are often installed in a series and precisely timed and sequenced to maximize their cleaning effectiveness based on individual process or material conditions.
The cost and frustration of ignoring the warning signs of developing problems is never more apparent than when things roll to a sudden halt, prompting a scramble to troubleshoot and correct conditions on the fly. None of us have the time in our day to deal with a broken-down truck, a shutdown conveyor, or a choked-up hopper. Don’t wait until it’s too late to address those sounds. Pay attention and take action. Give it a look or have it checked out and invest in proactive, preventative measures to keep your operation running smoothly.
comments