Problem
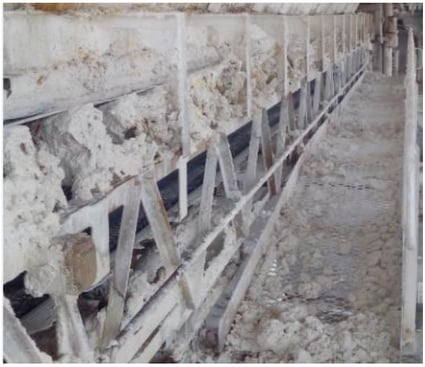
Imerys, the world's largest producer of talc, experienced carryback and spillage issues of kaolin paste on a conveyor at the RCC Brazil facility. A 60-inch (1,524 mm) wide belt transporting 330 TPH (300 MTPH) at a speed of 688 FPM (3.5 MPS) was spilling approx. 3.3 TPD (3 MTPD) along the length of the system. Inadequate belt cleaning allowed pasty material to stick to the belt and spread across the floor, creating a potentially dangerous work area. Material fouled pulley faces and gummed up idler bearings, requiring 3-4 workers to regularly replace rollers and clean around the system, which operators found potentially hazardous.
Solution
Martin Engineering was invited to offer solutions and consult on installing a new cleaning system with conveyor guards. Featuring a sturdy one-piece curved urethane blade, the Martin® QC1+™ Cleaner HD (Heavy Duty) uses the patented CARP™ (Constant Angle Radial Pressure) blade design to maintain effective cleaning through all stages of blade life. The unique polyurethane blend and tungsten carbide tip deliver service life 2-3 times longer than conventional urethane blades. The DT2S Reversing Secondary Cleaner features tungsten-tipped urethane blades suited for heavy-duty applications, installed on a track that slides into position on a rigid steel mandrel for quick blade replacement.
Results
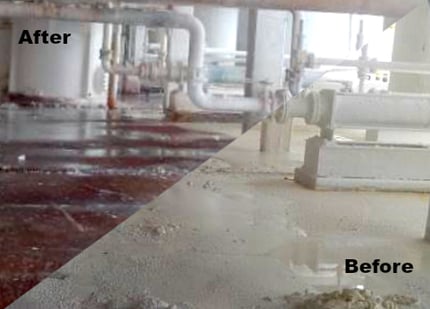
Operators describe the carryback and spillage problem as "completely solved," improving safety and reducing cleanup costs. Equipment costs for idlers and pulleys have been reduced, and service can be performed during scheduled downtime. Product loss has been reduced dramatically. Martin Engineering Brazil has been retained to periodically perform maintenance on the system to extend its operational life. Operators are currently in the planning process for the installation of similar solutions on other conveyors throughout the facility.
More Categories
- Material Spillage (35)
- Material Carryback & Belt Cleaning (32)
- Material Flow Problems (30)
- Dust & Material Spillage (23)
- Air Cannons (13)
- Conveyor Belt Component Damage (12)
- Dust (12)
- Conveyor Belt Mistracking (11)
- Safety (10)
- Basics of Belt Conveyor Systems (9)
- Belt Conveyor Safety (9)
- Vibration (8)
- Belt Conveyor System Maintenance (7)
- Dust Management (7)