Problem
Koda Energy was battling significant buildup problems. “Efficient material flow is a critical element of biomass-fired boilers, and accumulation or blockages can take a big bite out of a plant’s efficiency,” explained Martin Engineering Service Technician, James. "Ash buildup on furnace walls and tubes can choke the process, degrading equipment performance and introducing the potential for safety risks during cleanout." When maintenance crews noticed significant buildup, they first addressed the issue using a special fuel additive to reduce furnace fouling, but the results were disappointing. “We found the additive approach to be expensive and largely ineffective,” said Koda’s Chief Engineer and VP of Operations, Stacy Cook.
The company turned to manual cleanout techniques using an air lance. The method was more successful at removing the ash, but it required a daily work stoppage to complete the time-consuming process. “Daily air lancing did remove the buildup and helped us maintain full output, but we couldn’t reach all areas within the boiler,” Cook continued. “It also affected our production schedule and posed a potential safety risk for plant personnel,” he said. “To make matters worse, we were facing the possibility of a monthly shutdown to thoroughly clean out the boiler.”
Solution
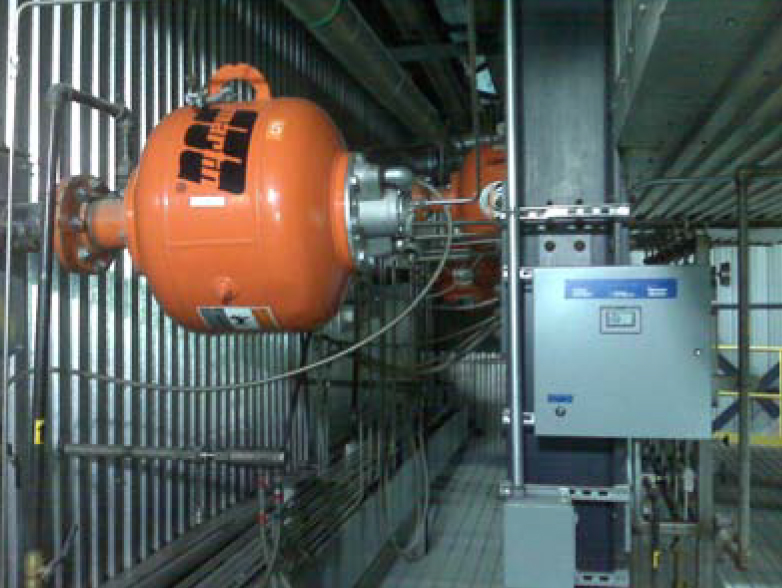
Over the course of three scheduled maintenance outages, Martin Engineering crews installed a total of 12 Martin® Hurricane Air Cannons. The high-powered air cannons blast air to dislodge accumulations and restore process flow. Introduced by Martin Engineering in 1974, air cannon technology has since developed a proven track record around the world for safely and efficiently relieving bottlenecks caused by material buildup.
Results
“Since the installation was completed, we’ve been able to maintain full boiler output without any hand lancing,” said Cook. “That has allowed us to keep the boiler wall surfaces clean, while avoiding the manpower requirements and potential hazards associated with hand lancing. We can now run the system at its rated capacity, without the negative effects previously posed by boiler fouling.” The upgrade was so successful that the Minnesota High Tech Association (MHTA) named General Mills and Koda Energy (partners in an environmentally friendly energy project) as finalists in the Innovation Collaboration of the Year category for the Tekne Awards. The Tekne Awards recognize Minnesota companies and individuals who have shown superior technology innovation and leadership.