
By Tim P. O'Harran on Jun 26, 2020 11:41:28 AM
When I'm out in the field, I get asked this question a lot. My answer isn't always short and sweet because conveyor maintenance can be more complex than you think. But here is my best shot at a quick summary.
#1 Frequent, thorough inspections of the entire conveyor system by well-trained and experienced personnel
Conveyor performance problems and safety issues can frequently be traced to improper installation or insufficient maintenance. Using a factory-trained specialty contractor (also known as ‘certified contractor’) for installation and ongoing maintenance contributes to safer and more efficient production with less unscheduled downtime and in the long run saves money and reduces injuries.
Mine, plant, and mill operators are increasingly turning to outside contractors to take advantage of consistent maintenance schedules and expert service. Conducted by experienced and highly-trained technicians, these contracts have been found to improve safety and help control costs. Specialty contracting may be a better choice (and is in my opinion) for service than internal resources since the providers are fully trained on the newest equipment designs and safety procedures. This approach to conveyor maintenance relieves the operators of having to stock spare parts and conduct ongoing inspections. In many cases, specialty contractors can quickly secure replacement equipment during periods of unscheduled downtime due to their industry-wide contacts.
#2 Maintenance service contracts deliver the best ROI through a series of factors
- Compliance – Prior to performing regularly-scheduled maintenance, the contractor may point out compliance issues and offer solutions. This avoids expensive fines and violations that could result in excessive downtime.
- Injuries / Liability – Working in several locations, contractors avoid the “comfort factor” and rely on a strict set of safety procedures to conduct maintenance. This minimizes injuries and their effect on insurance premiums while reducing liability.
- Efficiency – Maintenance service contracts focus on improving and sustaining uptime with the least capital investment possible.
- Consistency – Contractors have a clear directive and are not affected by internal factors (labor disputes, morale, etc.). The priority is maintaining safety and production levels while preserving the customer relationship.
- Cost of Operation – With a defined scope of work on a set budget along with clear reporting and recommendations on pending needs, operators can better forecast improvements and control labor costs, further improving ROI as time passes.
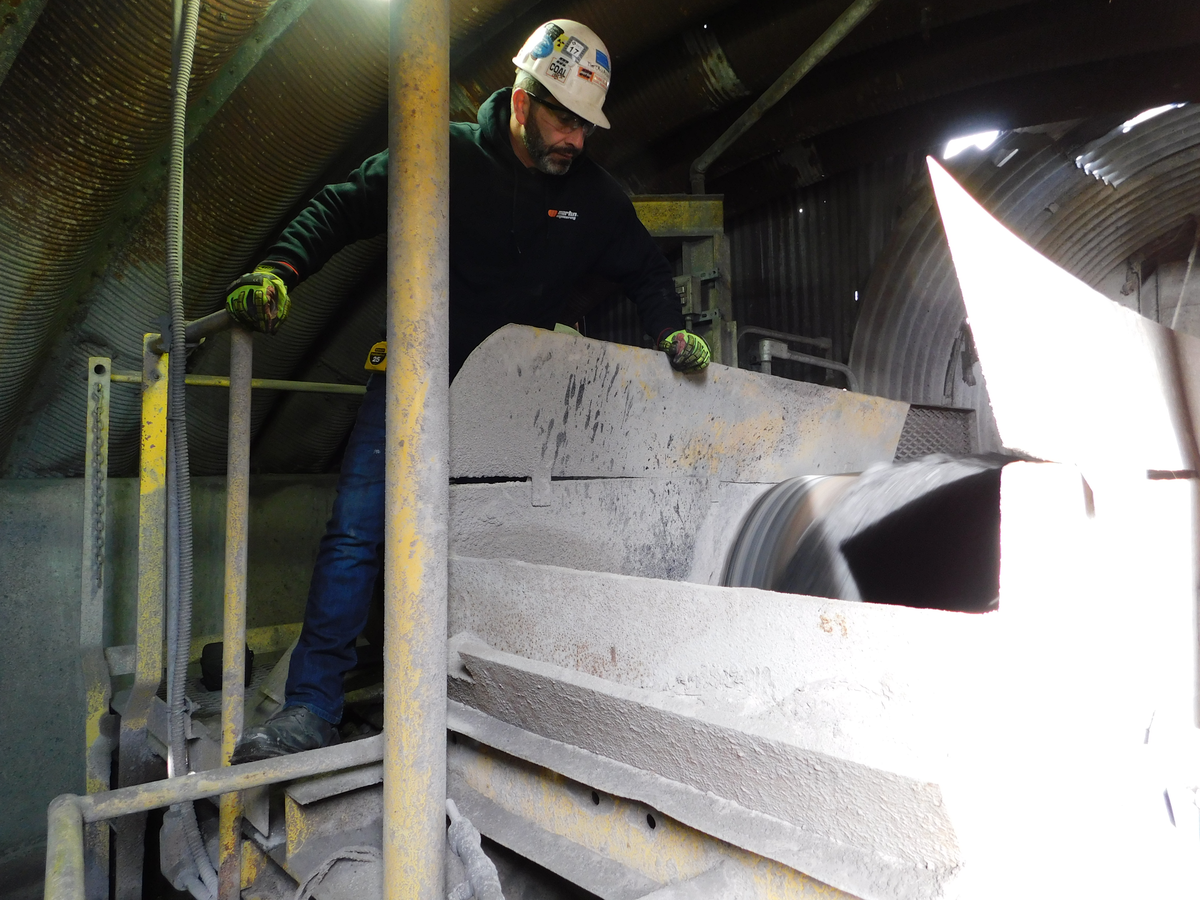
What are the elements of conveyor maintenance that don’t get proper attention?
All elements of a conveyor system require frequent inspection and preventive maintenance by trained personnel. Unfortunately, this doesn’t happen as often as it should. Instead, mine, plant, and mill operators typically react to breakdowns and fugitive material, paying the price in the long run.
Belt cleaners are a good example of components that suffer from insufficient maintenance and the ensuing problems multiply to other areas. An under-performing belt cleaner leads to carryback on the belt and accumulating spillage on other components which affects both their performance and service life. In addition to the necessary cleanup of spillage -- which often places employees in dangerous proximity to a moving conveyor -- fugitive material can negatively impact belt tracking, chute sealing, idler performance and longevity, air quality, and employee morale. Cleanup wastes valuable manpower and may cause the loss of valuable cargo.
Many belt cleaner systems are simply installed and forgotten. A survey of technicians indicates that only about 25% of installed belt cleaners are properly maintained. The vast majority of these cleaners are basic mechanical scrapers. While the initial cleaning results may be significantly better than no cleaner at all, lack of inspection and maintenance results in accepting a gradually lower level of effectiveness, a higher level of operating cost, and increased exposure to the hazards associated with cleaning up carryback. Truly effective belt cleaning starts in the design stage with adequate space for belt cleaners and positioning of work platforms for ergonomic inspection and maintenance access. Belt- and service-friendly designs improve production, reduce accidents, and prolong the life of the equipment.
To what extent does proper maintenance -- or lack thereof -- impact the overall operational picture?
comments