
By Seth Mercer on Oct 18, 2024 12:09:15 PM
Normally, spilling something is a minor inconvenience and nothing a paper towel or two can't handle. You know the saying, "no use crying over spilled milk." However, bulk material spillage is much more than an inconvenience. Fugitive material from belt conveyors can lead to significant issues, including violation of the Mine Safety and Health Administration (MSHA) housekeeping standards. In fact, housekeeping violations are the 7th most common citation written. Below are some key points outlining the connection.
MSHA Housekeeping Regulations
MSHA enforces strict housekeeping regulations under 30 CFR 56/57.20003 to maintain clean and safe work environments in mines. Regulations require operators to keep work areas clear of debris, such as fugitive material spilled from conveyors, and hazardous materials that can impede safety or cause accidents.
Fugitive material takes many forms depending on its root cause and includes spillage from the carrying side of the belt due to inadequate sealing and support, carryback on the underside of the belt due to ineffective belt cleaning, and airborne dust from the transfer point due to unsuccessful sealing and airflow management.
Material Spillage Risks
Spillage from belt conveyors commonly occurs when materials being transported overflow, leak, or escape due to belt misalignment, poor support and/or sealing, or worn-out components and equipment.
- Slips, Trips, & Falls: Spillage can accumulate around walkways, equipment, and working areas, creating uneven surfaces and increased risks of slips, trips, and falls. Loose material on walkways and platforms can cause workers to lose footing while walking/working.
💰 Read more: A Hole In The Bucket: True Cost of Material Spillage From Conveyors
- Restricted Access: Spillage in work areas can block access to emergency exits, equipment controls, and inspection areas, potentially creating additional violations.
- Fire Hazards: In coal or combustible-material mines, spillage increases the risk of fire, especially near conveyor motors and electrical equipment. In underground coal mines, the accumulation of combustible materials (30 CFR 75.400) was the most frequently cited violation in 2023.
Connection to MSHA Violations
Accumulated spillage often results in citations from MSHA inspectors under housekeeping rules, as it directly impacts the safety and cleanliness of work areas. As previously noted, housekeeping violations are one of the most frequent citations. Not only is it likely top-of-mind for most inspectors, but fugitive material is easy to spot and represents low-hanging fruit for inspectors who begin taking notes and writing citations.
📈 Read more: Stubble & Spillage Grow Slowly But Bring Big Changes
MSHA inspectors focus on areas where spillage can interfere with safety protocols, including conveyor transfer points, loading and unloading areas, and chutes and hoppers. Violations can lead to financial penalties, increased regulatory attention, and potentially forced shutdowns to address compliance issues.
Impact of Spillage on Conveyor Efficiency
Material spillage not only leads to MSHA violations but also impacts operational efficiency.
- Increased Maintenance Needs: Spilled material can cause wear and tear on conveyor components, causing premature failure and increased cleaning efforts.
- Reduced Productivity: Stoppages for cleaning and repairs due to spillage lower throughput and increase downtime while straining available resources and delaying other necessary maintenance.
Preventive Measures to Avoid MSHA Violations
- Engineering Controls: Implementing proper belt alignment, belt support, and skirting sealing systems will minimize material spillage. Installing industrial vibrators or belt cleaners at conveyor transfer points helps prevent material build-up on belts. By minimizing carryback, accumulated material spillage beneath the belt and build-up on idlers and conveyor structure is reduced, mitigating excessive wear and tear on the belt and components as well as time spent cleaning up.
💡 Read more: All Rolling Conveyor Components Steer The Belt
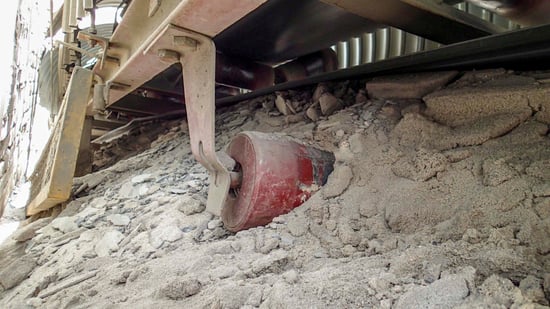
- Preventative Maintenance: Regular inspections and maintenance programs address potential spillage issues before they become safety hazards. Preventative maintenance is the most efficient and effective way to address the root causes of material spillage and avoid digging yourself out of a mess—both figuratively and literally.
- Employee Training: Training employees to recognize and promptly address spillage maintains compliance with MSHA standards. In order for preventative maintenance to be effective, employees who maintain belt conveyor systems must be knowledgeable and able to recognize the adverse conditions and root causes that lead to excessive material spillage.
Martin Engineering offers free belt conveyor system inspections as well as numerous conveyor operations and maintenance training options and resources. For more information about Walk The Belt™ Conveyor Inspections, click here.
📋 Read more: The 9 Most Critical Points of Belt Conveyor Inspection
Consequences of Non-Compliance
Fines, operational delays, and potential accidents related to poor housekeeping increase both regulatory and operational costs.
Persistent non-compliance with MSHA housekeeping regulations may lead to more severe penalties and scrutiny, harming the mine’s reputation and safety record.
By maintaining spillage-free conveyor systems, operators can avoid MSHA housekeeping violations and ensure a safer, cleaner, and more efficient operation. The next time you have to cleanup a spill, whether at home or work, think of how it can be prevented in the first place to save you time, energy, and money.
comments